ProSweets sets major focus on hygienic systems forging functional confectionery
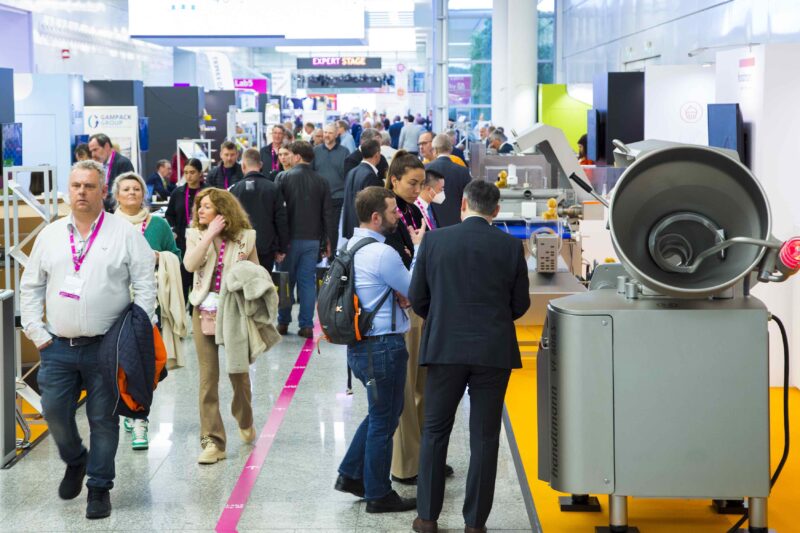
ProSweets 2023 was held as a special, shortened edition. Pic: Koelnmesse
Among the hottest topics for discussion at this year’s ProSweets will be the delivery of efficient and hygienic depositing systems for functional confectionery ranges, according to the show’s organisers, writes Neill Barston.
According to the the Koelnmesse team, final preparations for the event are in full flow (see our exclusive preview video here), with sustainable production methods and ever-more rapid cycles of innovation also set to feature strongly for this year’s show staged alongside ISM, between 28-31 in Cologne, Germany.
As the event team noted to Confectionery Production, with more than 250 exhibitors expected for ProSweets, and over 1,400 businesses from around the world at ISM, it will be anything but dull for the 2024 event, which is set to feature some strong new additions.
According to the event’s management team, it observed a notable continuing trend for sweets developed with active ingredients, as well as the creation of hygienic systems for starchless depositing in order to accommodate the growing demand for functional products.
Whether vitamins, Omega-3 fatty acids or minerals – the offer of sweets with highquality nutraceuticals has grown rapidly over the past years. In the year 2022, the turnover for OTC (over the counter) products available without a prescription increased by around ten percent up to over Euro ten billion in Germany alone.
This corresponds to around a fifth of the overall European turnover. Fruit gums and boiled sweets will represent an even more significant market share in the pharmaceutical section in future, because with their popular texture and diversified shapes they are increasingly replacing the classic chewable tablets. A trend that will be reflected by a new generation of systems for powderless production at ProSweets Cologne. A number of which are not only suitable for the production of chocolate or jelly items, but also available as a production system for OTC sweets based on pectin, gelatine, starch, carrageenan or agar-agar.
As well as being used for the production of masses with a high dry substance content and viscosities, the modern lines enable moulding in reusable moulds, whilst at the same time complying with the highest hygiene standards. The focus lies on the precise dosing of functional additives to ensure the right active ingredients content per individual product.
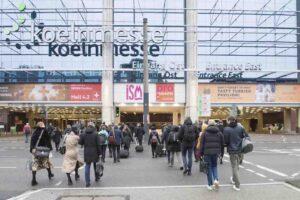
Eingang Ost
Growth in OTC ranges
Furthermore, as Koelnmesse added, demands in process reliability for the production of OTC products are particularly high when pharmacologically active ingredients such as acetylsalicylic acid or paracetamol are processed. Complete solutions for the powderless production Since the classic production with moulding starch doesn’t satisfy the strict GMP regulations, Winkler und Dünnebier Süßwarenmaschinen (WDS) orientates itself on the hygienic design criteria typical for the pharmaceutical industry. WDS has developed a technique for moulding in polycarbonate moulds especially for the production of OTC fruit gums on ConfecECO and ConfecPRO machines.
In addition, another prominent exhibitor will be Hänsel Processing also provides solutions for sweets producers, who process OTC supplements and nutraceuticals in both liquid and powder form. The company has succeeded in developing a fully-integrated process plant, the Sucroliner, which processes the sweets masses with a low residual water content. Special attention is paid here to the hygienic design of the process plant with its stainless steel execution and fully-integrated CIP cleaning (cleaning in place). Modern OTC production lines like the 800 Robotic NS that Tanis offers have a capacity of up to 290,000 fruit gums and jelly beans an hour.
The robot-controlled line is recipe-controlled and thus automatically adjusts itself to ensure an optimally synchronised process. The single tray transport and the servo positioning drive guarantee a smooth process from the moulding through to the extraction from the moulds. With its NutraFlash, Syntegon also takes an holistic turnkey approach that ensures a closed-loop production. The business will be showcasing a full range of its equipment solutions at this year’s show.
After pouring the mass into reusable plastic moulds, the products cool down in the integrated cooling unit. This closed cycle saves manufacturers additional manual steps, like the removal of the moulds and cooling the products down in external cooling chambers.
Machines that satisfy the highest hygiene demands But not only the manufacturers of OTC products have to observe the highest standards regarding hygiene. Regardless of whether fruit gum and jelly items, toffees, caramels or fondant are being processed: the lower the contamination risk the safer the production is and the higher the product quality. How clean a plant is after the cleaning process depends above all on the condition of the surfaces. Stainless steel is generally considered to be “the” hygienic material per se. It is essential here that the areas of the machines and pipes that come into contact with the products are good quality. The passivity of the stainless steel and a medium surface roughness of max. 0.8 micrometres ensures this.
The layout of the modern production and packaging systems that are presented at the Cologne fair grounds is based on an established principle: The more open the design, the easier the cleaning is. The processing of products that like chocolate cause heavy soiling, is not a problem because all surfaces of the machinery are easily accessible and suitable for wet cleaning. For the processing of products that contain allergens, such as nuts or bakery products that contain gluten, the sweets and snacks producers also have the opportunity to install special hygiene belts that allow the usage of mobile belt cleaning devices.
Beam’s BEbelt for example was especially developed for the demands of belt cleaning in systems used for the production of chocolate and filled chocolates. The steam cleaner is designed so that first of all a scraper and a cleaning brush mounted at the front remove the worst of the dirt on the moving belt. Then, the steam removes the remaining product residues. These are ultimately vacuumed up and bound in the waste water filter. This is how sweets manufactures can simplify the cleaning processes and minimise downtimes.